Company
About us & Mission
CAM was founded in 1984 as a small-scale workshop in the heart of Carmagnola (TO), established by the Tuninetti family, setting off on an adventure by overhauling cylinders, constructing tools and simple details for Fiat Teksid Carmagnola and Fiat Ferroviaria Savigliano.
In the 1980s and ’90s, the company went on to specialise in the construction of manual and automatic mechanical equipment, as well as in the processing of medium-large bodywork sub-assemblies. Since the 2000s, CAM has evolved considerably in the field of industrial automation and integration of complete processes in the automotive and aerospace sectors.
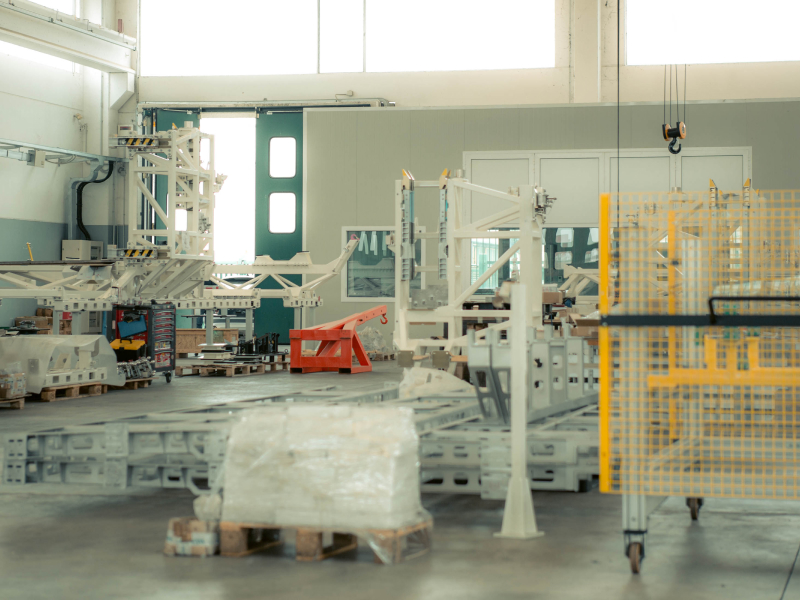
The company has grown steadily over time, and, since 2020, has entered a new important phase of expansion thanks to a strong diversification, with a view to differentiating the business and internationalisation. Combined with a strong entrepreneurial spirit of the founders, this growth and maturation has allowed us to constantly invest in people, innovation and equipment, all whilst maintaining and strengthening relationships of trust and partnership with our clients, thanks to the service quality and reliability.
- A strong capacity for proposing means of developing robust and efficient alternative solutions;
- Proficiency in different joining and manufacturing technologies;
- Marked process control with a maximisation of internal activities, translating to transparency for the client during all phases of the project;
- Effective mix of qualified resources and junior talent with low turnover, with the team able to manage complex projects in the language and per the specifications of the client;
- Space to perform a preliminary installation and produce a first batch of components in-house;
- Functional guarantee and reliable commissioning, thanks to a complete installation and pre-testing of the CAM systems;
- Strong drive for innovation.
The spirit of partnership and the desire for constant development and knowledge are the fuel that powers our work each and every day.
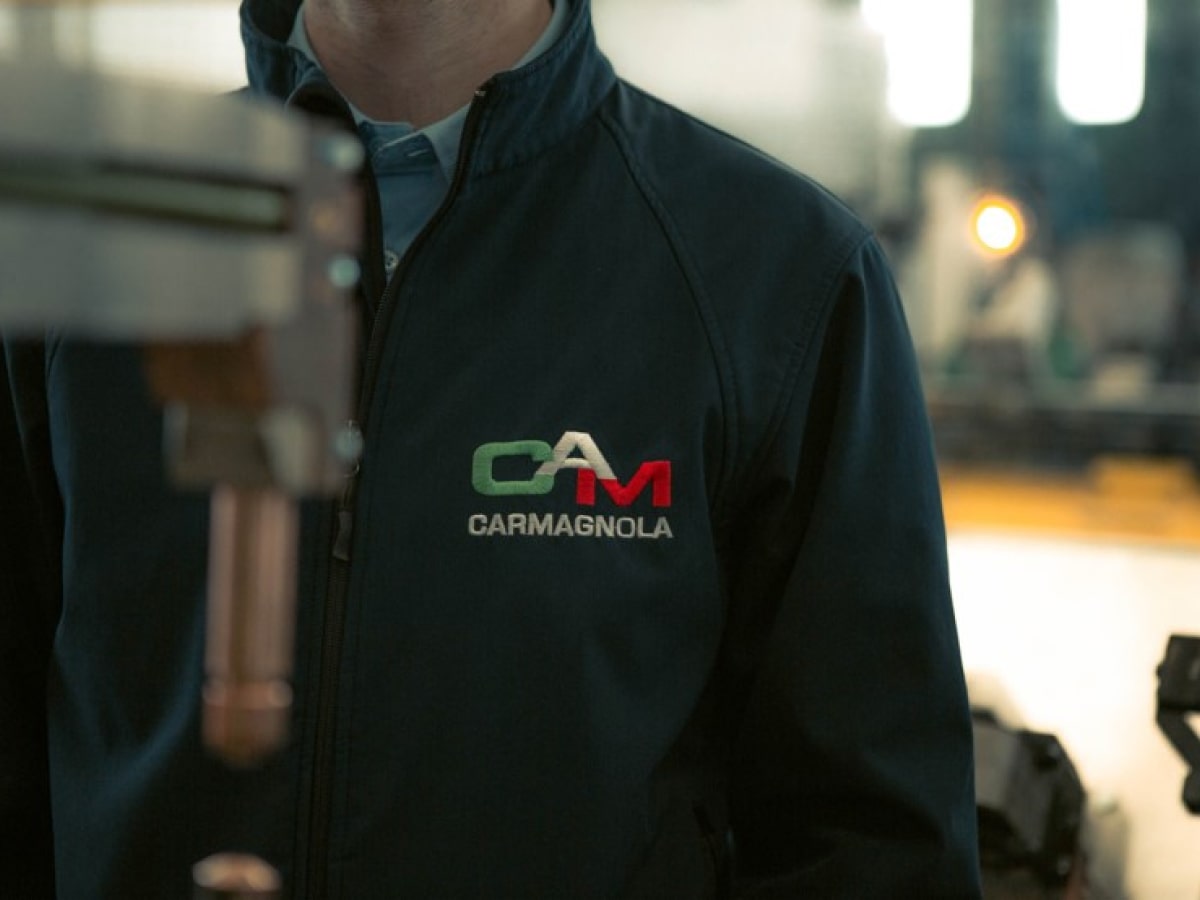
Organisation, production process and capacity
We work mainly on projects, with solutions targeted to the specific requirements of the client.
- Automotive and General Industry
- Aerospace
During the offer phase, multiple technical solutions are developed in order to identify the technical/commercial solution that best meets the client’s needs. Each work team is composed of a commercial structure, one or more Project Designers and a Cost Estimator.
Once an order is acquired, for both BUs, ‘deliveries‘ are made from the Sales Team to the Project Team, composed of a Project Manager, a Mechanical Technical Leader, a Technical Leader for ‘controls’ and a Production/Site Manager. The Project Team takes charge of the project, performs a more in-depth analysis of the technical solution provided for in the project outline and the relative costs and times, then activates the engineering body for execution of the mechanical and plant design. A dedicated CE Documentation and Certification Team collaborates with the Quality body and processes in parallel the necessary documentation in compliance with European regulations and the requests of each client.
Once the design phase is completed comes the construction of the plant components, mainly carried out in our production plants (with 2,500 m² of indoor space).
The machining and mechanical construction and pre-testing activities are carried out on state-of-the-art machinery that covers all production steps.
The machine tools and measuring devices are connected to the company computer network in order to guarantee maximum efficiency, exploiting the possibilities offered by CAD/CAM systems and the 4.0 philosophy.
Subsequent installation and commissioning/in-house testing are carried out in as many dedicated areas (with 4,500 m² of indoor space) until pre-testing.
In accordance with the BU, dedicated teams deal with the installation in CAM of the plant or station along with the subsequent commissioning phases (mechanical, electrical, software and robots) until adequate tests and pre-tests are carried out in CAM, in the presence of clients.
We can develop over 240,000 h/year of activities solely in CAM!
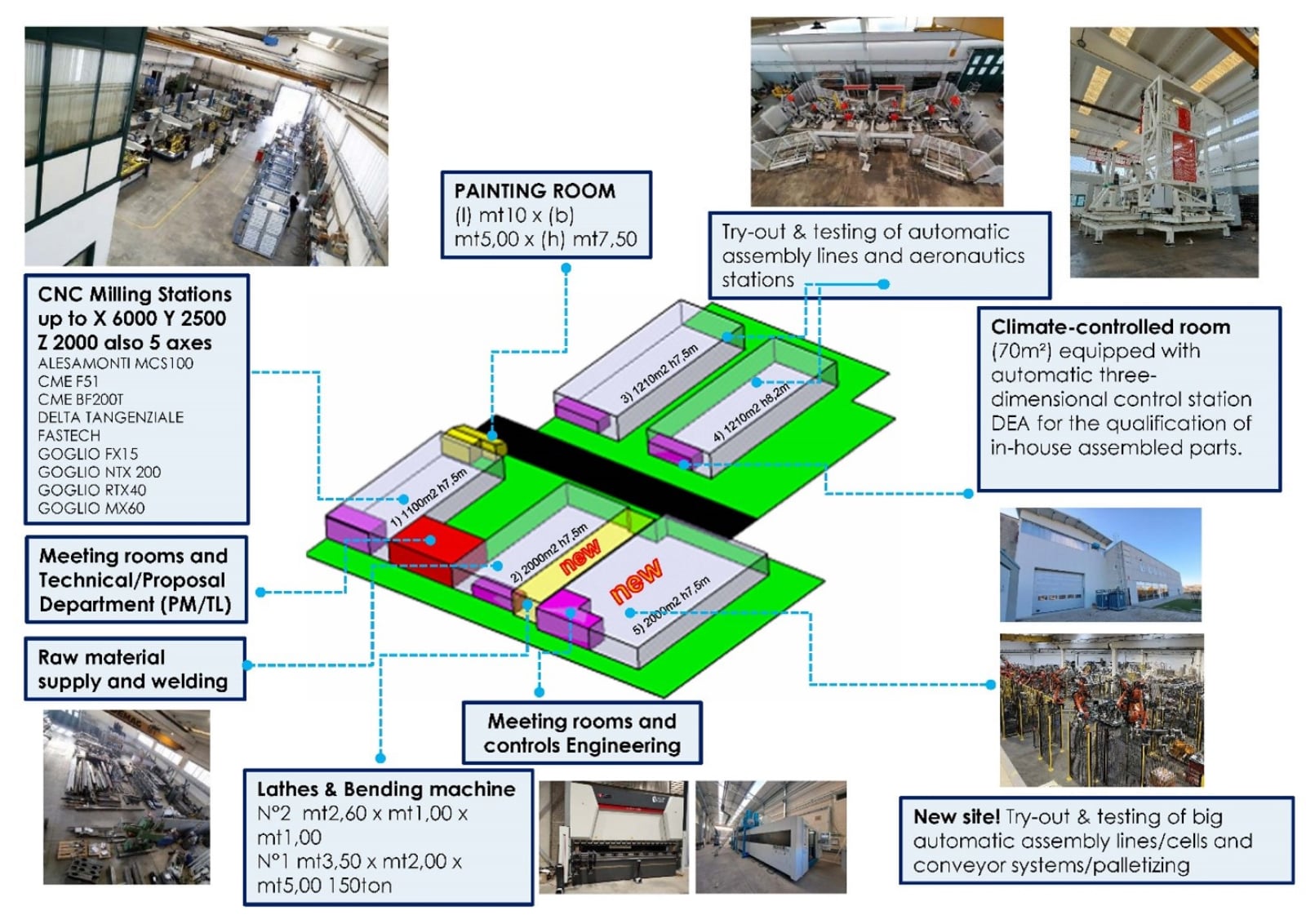
Following positive results from the pre-test in CAM, the systems are disassembled and shipped to the site, where CAM specialised personnel – mainly the same people who carried out the in-house pre-test – conduct reassembly, commissioning and production start-up up until being accepted by the end client.
Certifications and Quality
From the get go, it has been fundamental for CAM – as the basis of its growth strategy – to be a quality supplier with a flexible and dynamic organisation.
The current integrated Quality Management System is structured in accordance with the following regulations or procedures:
- ISO 9001:2015 – Quality;
- ISO 3834 – Welding;
- TiSAX (coming soon).
Certificate ISO 9001:2015
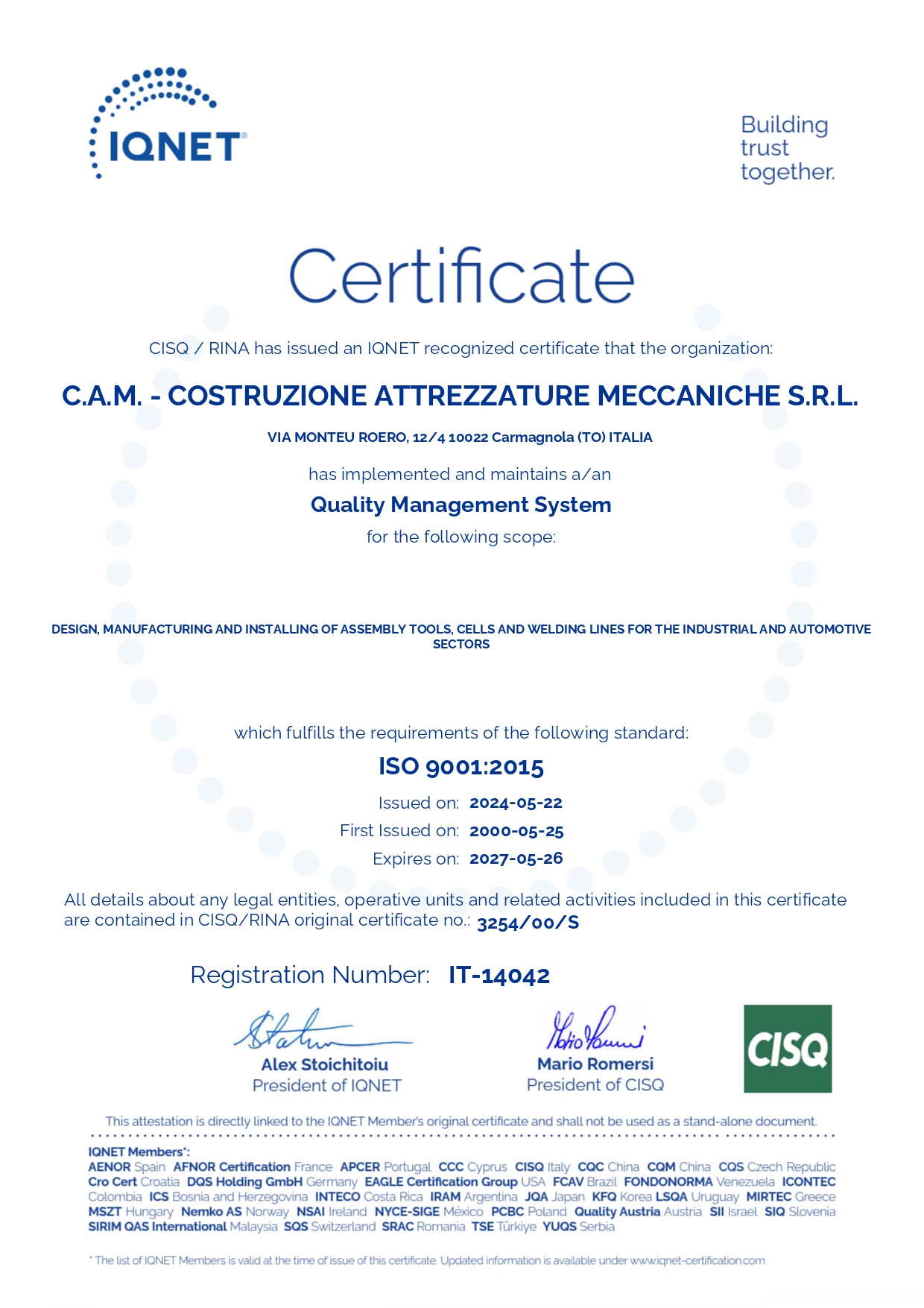
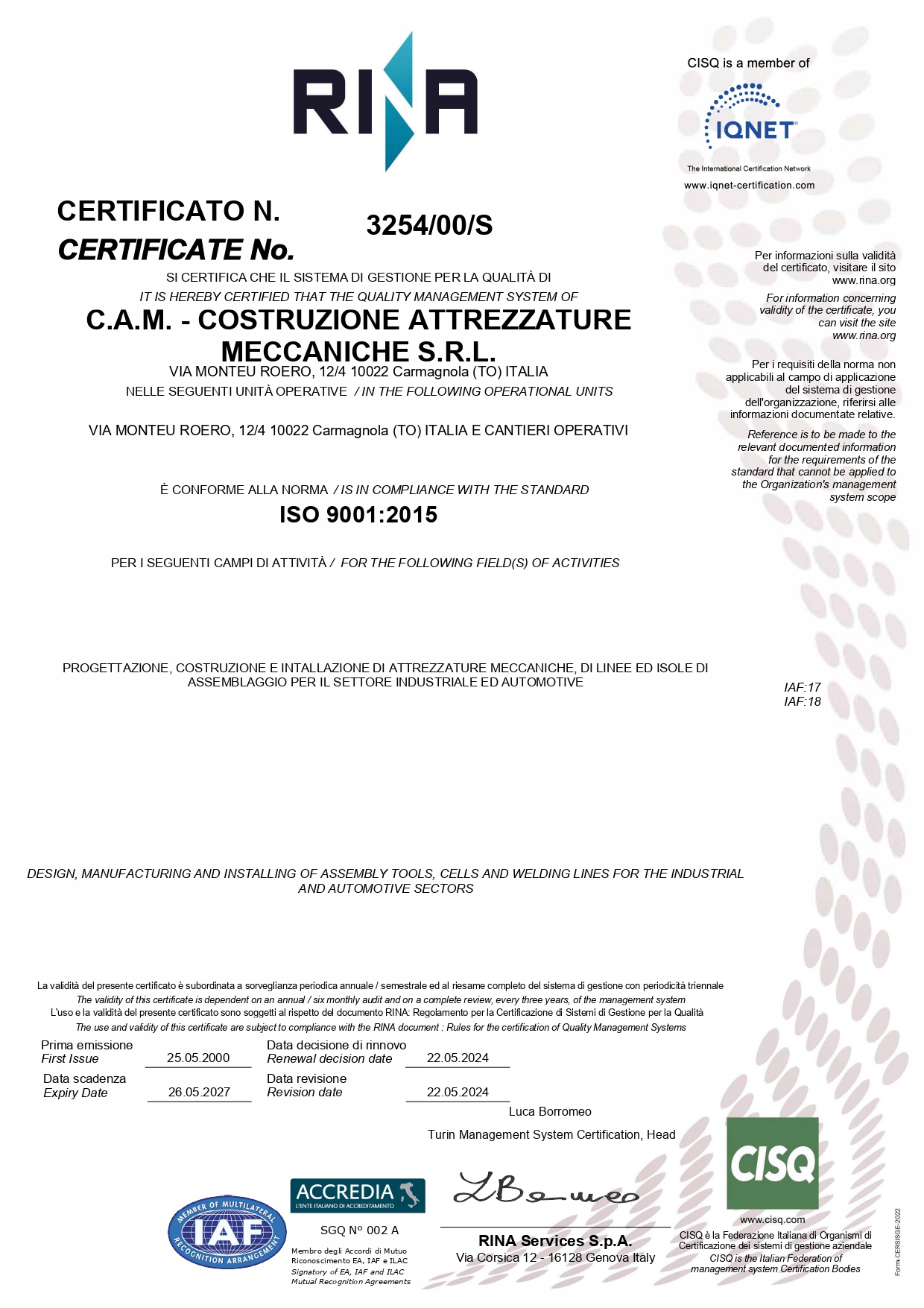
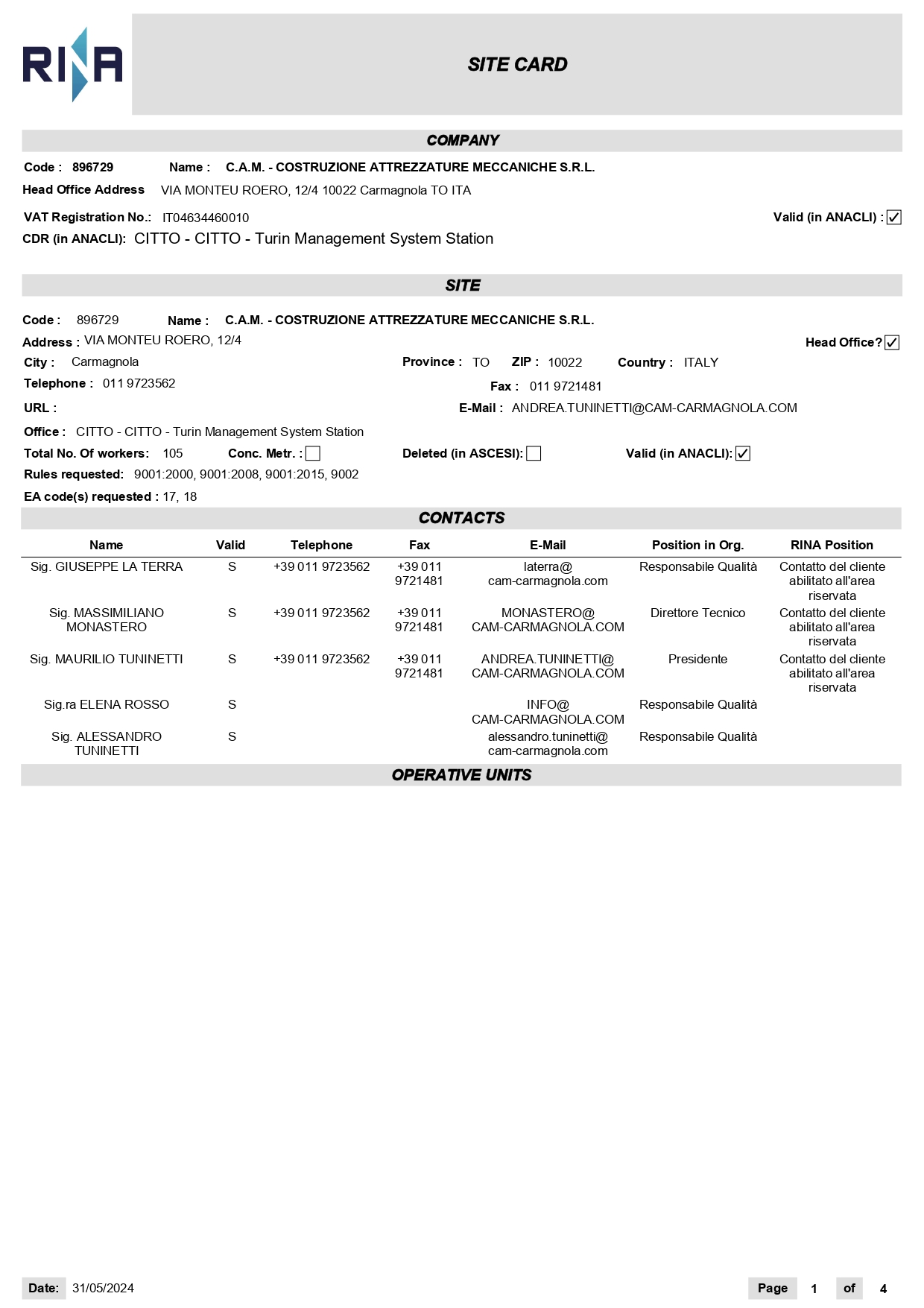
Certificate UNI EN ISO 3834
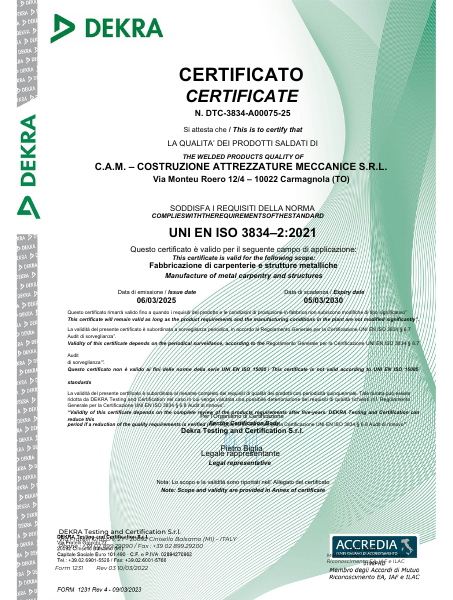
Certificate TISAX
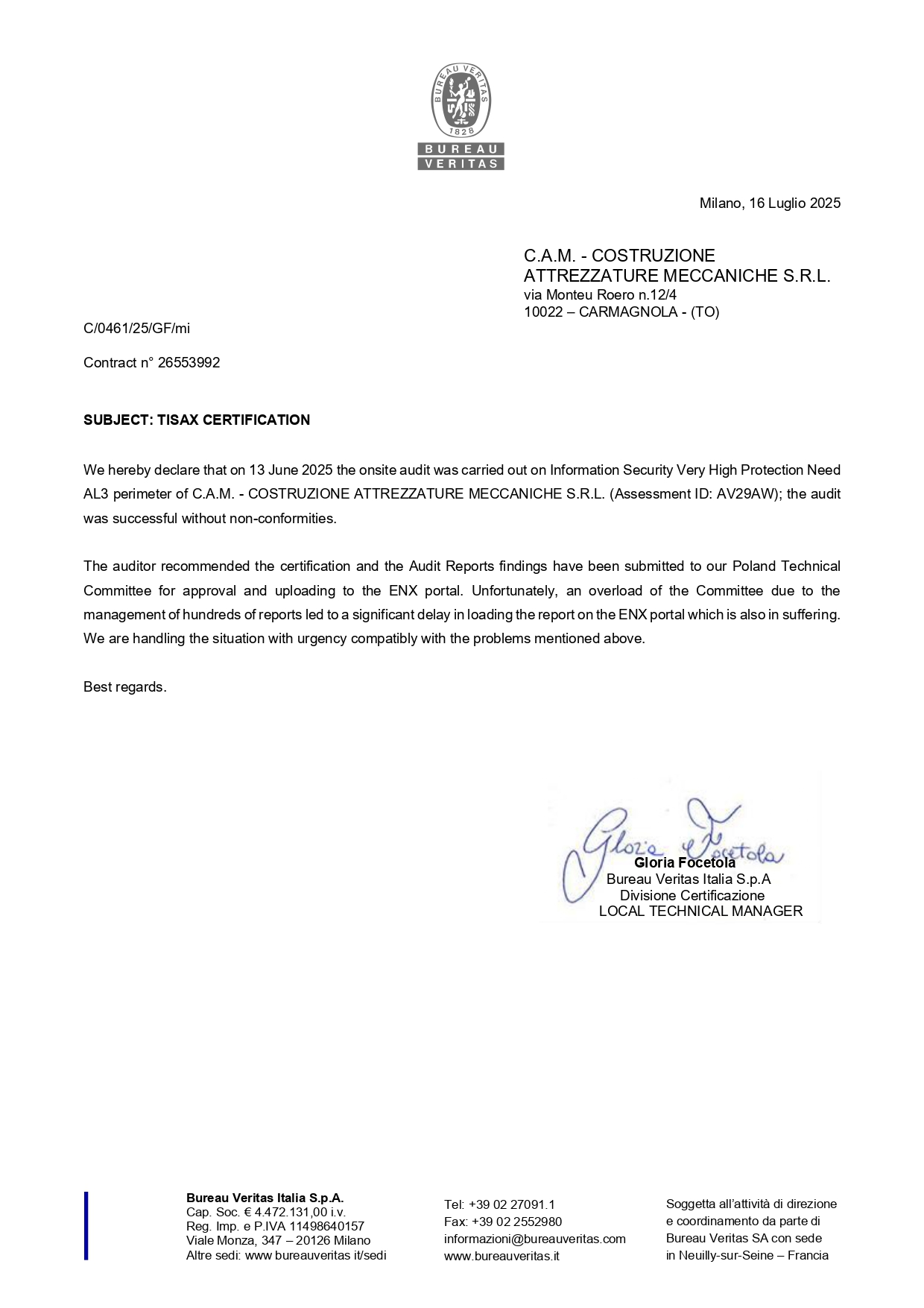
Sustainability Certificate
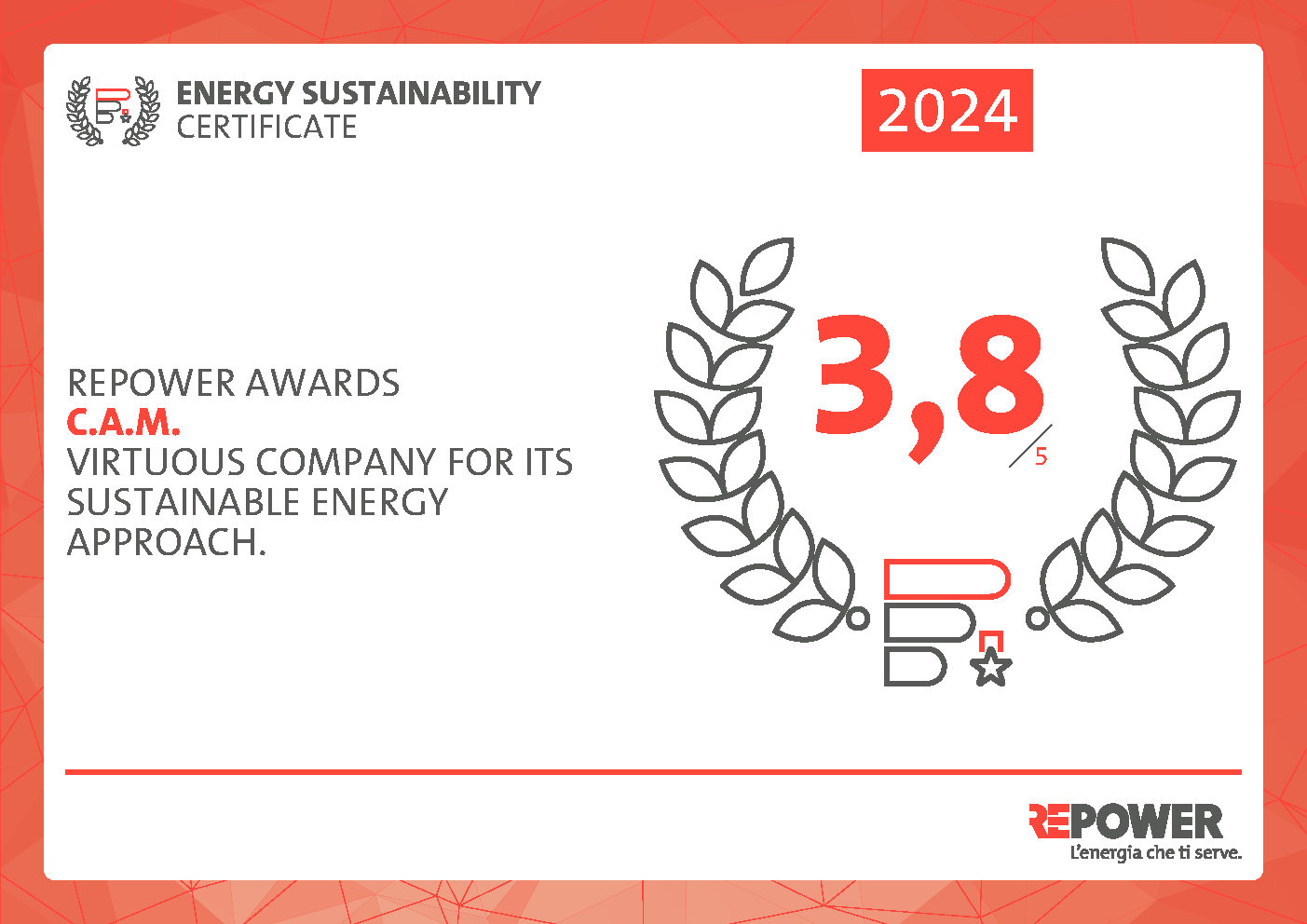
To date, the system applies to the “Design, construction and installation of mechanical equipment, assembly lines and islands for the industrial and automotive sectors”.
Today, the company’s Quality System – oriented towards strong sustainability and respectful of procedures and the ESG approach – is managed internally, being a mature and well-established device adopted in every functional area of the company, in pursuit of constant improvement and optimisation in accordance with the spirit that has always guided the company.
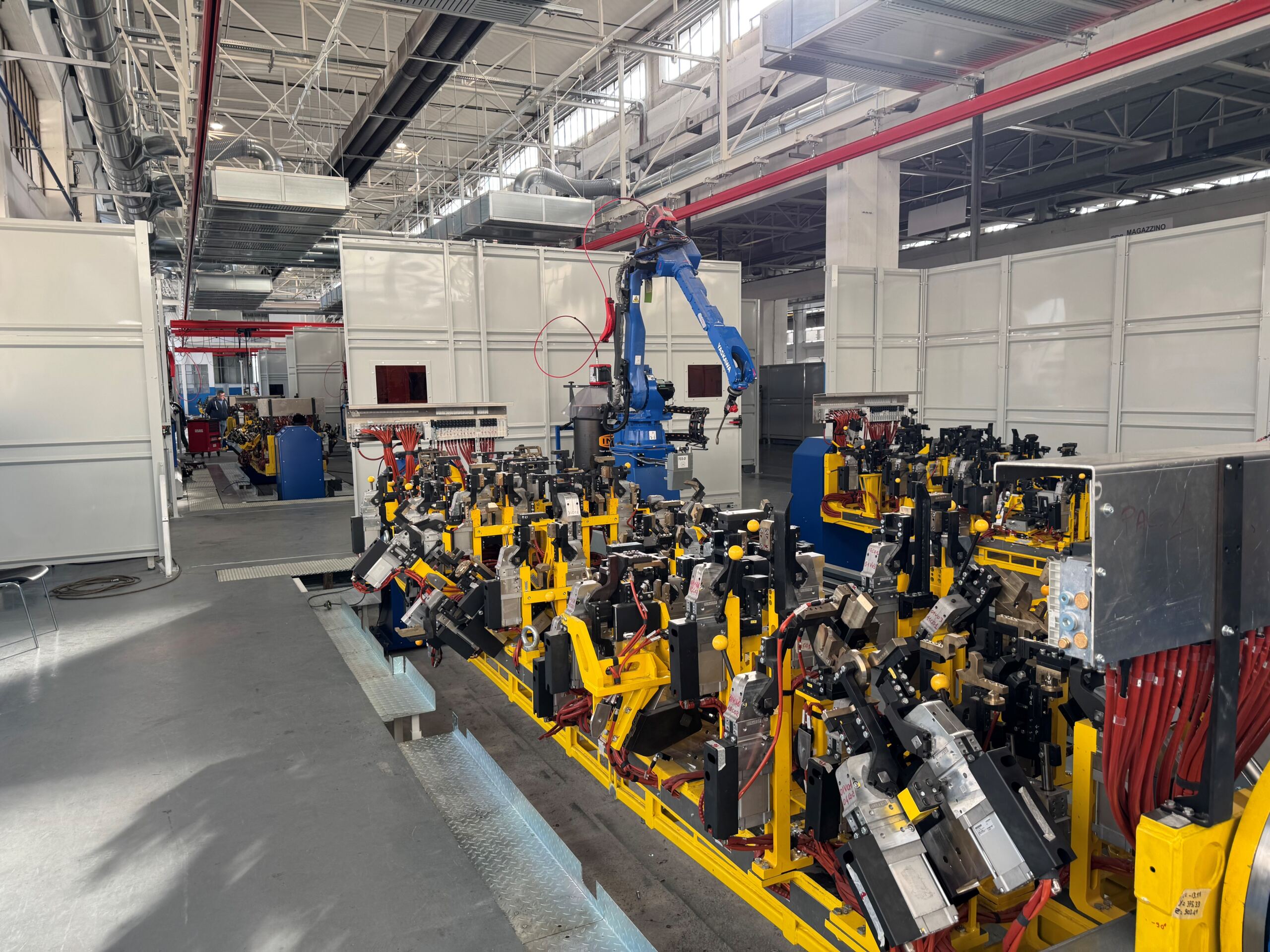